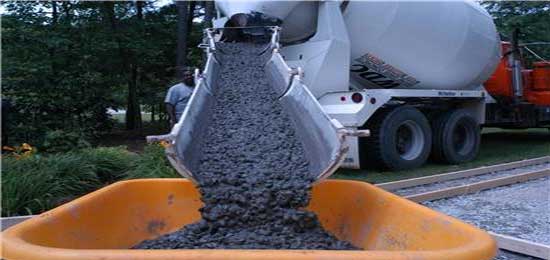
Transportbeton (RMC) ist eine Art von Beton, der in einer Zementfabrik hergestellt wird, oder speziell als Mischanlage bekannt, nach einem bestimmten Satz von Proportionen, und dann an eine Baustelle geliefert, von LKW mit Mischern montiert. Dies führt zu einer präzisen Mischung, mit der Spezialbetonmischungen entwickelt und auf Baustellen eingesetzt werden können. Die erste Fabrik, die Transportbeton produzierte, wurde in den 1930er Jahren gebaut; die Branche begann jedoch erst Ende der 80er Jahre zu expandieren. Seitdem ist es weiter deutlich gewachsen.
Fertigbeton wird manchmal dem Betonmischen vor Ort vorgezogen, da das Volumen mit der Genauigkeit des Anteils der Mischungen und auch aufgrund der verringerten Verwirrung auf der Baustelle erzeugt werden kann. Die Verwendung einer vorgegebenen Betonmischung reduziert die Flexibilität sowohl in der Lieferkette als auch in den tatsächlichen Komponenten des Betons.
Transportbeton wird auch als kundenspezifische Betonprodukte für gewerbliche Zwecke bezeichnet. Transportbeton (RMC) bezieht sich auf Beton, der speziell für die Lieferung an die Baustelle des Kunden in einem frisch gemischten und / oder ungehärteten Zustand hergestellt wird. Beton selbst ist eine Mischung aus Portlandzement, Wasser und Zuschlagstoffen aus Sand und Kies oder Schotter. Auf traditionellen Baustellen wird jedes dieser Materialien separat beschafft und in bestimmten Anteilen vor Ort gemischt, um Beton herzustellen. Transportbeton wird nach Volumen gekauft und verkauft – normalerweise ausgedrückt in Kubikmetern (Kubikmeter in den USA).
Transportbeton wird unter kontrollierten Bedingungen hergestellt und mit ausgeklügelten Geräten und Methoden transportiert und vor Ort platziert. Im Jahr 2011 arbeiteten 72.924 Arbeiter in 2.223 Unternehmen, die Transportbeton in den Vereinigten Staaten produzierten.
Inhalt:
- Prozess
- Vorteile
- Nachteile
- Volumetrischer Mischer
Prozess von Transportbeton
Transportbeton enthält Zement, Zuschlagstoffe, Sand, Wasser und andere Chemikalien, die in einer zentral gelegenen Anlage für eine erstklassige. Der Beton wird dann in Transportmischern zur Baustelle geliefert und kann ohne weitere Behandlung sofort verwendet werden. Die automatische Anlage überwacht die Dosierung, das Wasser-Zement-Verhältnis, die Dosierung der Beimischung und den Feuchtigkeitsgehalt mit Präzision, um Qualitätsbeton herzustellen.
Alle Zutaten, die zur Herstellung von Transportbeton verwendet werden, werden in einem gut ausgestatteten Labor, das an die Anlage angeschlossen ist, gründlich auf ihre Qualität und physikalischen Eigenschaften auf Konformität mit den einschlägigen internationalen Normcodes getestet. Die Feuchtesonde bestimmt den Wassergehalt im Sand und in den Zuschlagstoffen. Dies hilft dementsprechend bei der Festlegung des für die Herstellung der Mischung zuzugebenden Wasseranteils. Versuchsmischungen werden durchgeführt und getestet, um sicherzustellen, dass jede einzelne Betoncharge, die aus der Anlage kommt, verschiedene Mischungsdesigns gemäß den Anforderungen des Kunden mit unterschiedlichen Betonqualitäten erfüllt.
Vorteile von Transportbeton
Im Folgenden sind die Vorteile von Transportbeton:
- Transportbeton (RMC) ermöglicht einen schnellen Bau durch programmierte Lieferung vor Ort, mechanisierten Betrieb mit konsequenter Wirtschaftlichkeit.
- RMC reduziert die Arbeitskosten und die Kosten für die Baustellenüberwachung.
- RMC kommt mit Konsistenz in der Qualität durch genaue & computergesteuerte Kontrolle von Sandaggregaten und Wasser gemäß Mischungsdesigns.
- Die Produktion von RMC hilft bei der Minimierung von Zementverschwendung durch Schüttgutumschlag.
- Die Produktion von RMC ist relativ umweltfreundlich.
- Reduzierte Projektzeit, was zu Einsparungen in allen Aspekten führt.
- Ordnungsgemäße Kontrolle und sparsame Verwendung von Rohstoffen, was zur Einsparung natürlicher Ressourcen führt.
Nachteile von Transportbeton
Im Folgenden sind die Nachteile von Transportbeton aufgeführt:
- Die Materialien werden in einer zentralen Anlage dosiert, und das Mischen beginnt in dieser Anlage. Daher ist die Fahrzeit von der Anlage zum Standort über längere Strecken kritisch. Einige Standorte sind einfach zu weit entfernt, wodurch die Gefahr besteht, dass Transportbeton durch Abbinden unbrauchbar wird.
- Es wird zusätzlichen Straßenverkehr erzeugen. Im Allgemeinen sind Fertigmischwagen groß und können viel Fläche auf der Straße abdecken, die anderen Verkehr blockiert. Darüber hinaus müssen Zufahrtsstraßen und Baustellenzufahrten das größere Gewicht des Transportwagens plus Ladung tragen können. (Grüner Beton ist ca. 2,5 Tonnen pro m3.) Dieses Problem kann durch den Einsatz sogenannter Mini-Mix-Unternehmen überwunden werden, die kleinere Mischer mit einer Kapazität von 4 m3 verwenden, die in der Lage sind, eingeschränktere Standorte zu erreichen.
- Die begrenzte Zeitspanne zwischen Mischen und Aushärten von Beton bedeutet, dass die Fertigmischung innerhalb von 210 Minuten nach dem Dosieren in der Anlage platziert werden sollte. Moderne Beimischungen können diese Zeitspanne genau modifizieren, jedoch ist die Menge und Art der Beimischung, die der Mischung zugesetzt wird, sehr wichtig.
Mobiler volumetrischer Mischer
Der mobile volumetrische Mischer kann eine gute Alternative zu Transportbeton darstellen. Dies ist ein hybrider Ansatz zwischen Transportbeton und traditionellem Mischen vor Ort. Der volumetrische mobile Mischer ist ein LKW, der Betonbestandteile und Wasser enthält, die auf dem LKW auf der Baustelle gemischt werden, um Beton entsprechend der benötigten Menge herzustellen und zu liefern. Das Mischen auf dem LKW auf der Baustelle beseitigt die Probleme von Transportbeton, z. B. Verzögerungen, die dazu führen können, dass der vorgemischte Beton unbrauchbar wird.