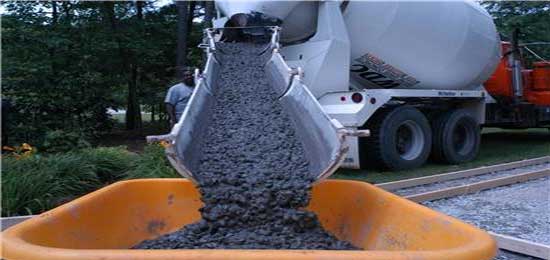
kant-en-klare beton (RMC) is een type beton dat wordt vervaardigd in een cementfabriek, of specifiek bekend als de batching fabriek, volgens een bepaalde set van verhoudingen, en vervolgens geleverd aan een werkplek, door vrachtwagen gemonteerd met mixers. Dit resulteert in een nauwkeurig mengsel, waardoor speciale betonmengsels kunnen worden ontwikkeld en geïmplementeerd op bouwplaatsen. De eerste fabriek die ready mix beton geproduceerd werd gebouwd in 1930; echter, de industrie begon niet uit te breiden tot eind jaren ‘ 80. sindsdien is het aanzienlijk blijven groeien.
stortklaar beton heeft soms de voorkeur boven het mengen van beton op de bouwplaats vanwege het volume dat het kan produceren met een nauwkeurige verhouding van de mengsels en ook vanwege verminderde verwarring op de bouwplaats. Het gebruik van een vooraf bepaald Betonmengsel vermindert de flexibiliteit, zowel in de toeleveringsketen als in de eigenlijke componenten van het beton.
stortklaar beton wordt ook wel de op maat gemaakte betonproducten voor commerciële doeleinden genoemd. Stortklaar beton (RMC) verwijst naar beton dat specifiek wordt vervaardigd voor levering aan de bouwplaats van de klant in een vers gemengde en plastic of onverharde staat. Beton zelf is een mengsel van Portland cement, water en aggregaten bestaande uit zand en grind of steenslag. In de traditionele werkplaatsen, elk van deze materialen wordt afzonderlijk verkregen en gemengd in bepaalde verhoudingen op de site om beton te maken. Kant-en-klare beton wordt gekocht en verkocht per volume-meestal uitgedrukt in kubieke meters (kubieke yards in de VS).
stortklaar beton wordt onder gecontroleerde omstandigheden vervaardigd en met behulp van geavanceerde apparatuur en methoden ter plaatse getransporteerd en geplaatst. In 2011 waren er 72.924 werknemers werkzaam in 2.223 bedrijven die Ready Mix beton produceerden in de Verenigde Staten.
inhoud:
- proces
- voordelen
- nadelen
- volumetrische menger
proces van stortklaar beton
stortklaar beton bevat cement, aggregaten, zand, water en andere chemische stoffen, die in een centraal gelegen fabriek worden gewogen voor een Premiumkwaliteit. Het beton wordt vervolgens geleverd aan de bouwplaats in transit mixers en kan direct worden gebruikt zonder verdere behandeling. De automatische fabriek bewaakt wegen-batching, water-cement verhouding, dosering van vermenging, vochtgehalte, met precisie om kwaliteit beton te produceren.
alle ingrediënten die worden gebruikt voor de bereiding van stortklaar beton worden grondig getest op hun kwaliteit en fysische eigenschappen in een goed uitgerust laboratorium dat aan de installatie is bevestigd om aan de desbetreffende internationale standaardcodes te voldoen. De vochtsonde bepaalt het watergehalte in het zand en aggregaten. Dit helpt dan ook bij het vaststellen van het aandeel water dat moet worden toegevoegd voor de bereiding van het mengsel. Proefmengsels worden uitgevoerd en getest om ervoor te zorgen dat elke partij beton die uit de fabriek komt voldoet aan verschillende mengontwerpen volgens de eis van de klant met verschillende soorten beton.
voordelen van stortklaar beton
Hieronder volgen de voordelen van stortklaar beton:
- Ready Mix Concrete (RMC) zorgt voor een snelle bouw door middel van geprogrammeerde levering op de site, gemechaniseerde werking met consequente economie.
- RMC verlaagt de arbeidskosten en de kosten voor het toezicht op de locatie.
- RMC wordt geleverd met consistentie in kwaliteit door nauwkeurige & geautomatiseerde controle van zand aggregaten en water volgens mengontwerpen.
- de productie van RMC helpt bij het minimaliseren van cementafval als gevolg van bulkverwerking.
- de produktie van RMC is vrij van verontreiniging.
- verkorte projecttijd resulterend in besparingen in alle aspecten.Goede controle en zuinigheid bij het gebruik van grondstoffen, wat resulteert in besparing van natuurlijke hulpbronnen.
nadelen van stortklaar beton
hieronder volgen de nadelen van stortklaar beton:
- de materialen worden gebundeld in een centrale installatie, en het mengen begint in diezelfde installatie. De reistijd van de fabriek naar de locatie is dus over langere afstanden kritisch. Sommige sites zijn gewoon te ver weg, die het risico dat kant-en-klare mix beton onbruikbaar kan worden als gevolg van de instelling.
- het zal extra wegverkeer genereren. Over het algemeen, klaar Mix vrachtwagens zijn groot in omvang en kan veel gebied in de weg blokkeren van ander verkeer te dekken. Bovendien moeten toegangswegen en toegang tot het terrein het grotere gewicht van de kant-en-klare vrachtwagen plus lading kunnen dragen. (Groen beton is ca. 2,5 ton per m3.) Dit probleem kan worden opgelost door gebruik te maken van zogenaamde “mini mix” -bedrijven die kleinere 4m3-capaciteitsmixers gebruiken die beperktere locaties kunnen bereiken.
- de beperkte tijdspanne tussen mengen en uitharden van beton betekent dat kant-en-klaarmengsel binnen 210 minuten na het batchen in de installatie moet worden geplaatst. Moderne toevoegingen kunnen wijzigen die tijdspanne precies, echter, de hoeveelheid en het type van de toevoeging aan de mix is zeer belangrijk.
volumetrische mobiele menger
volumetrische mobiele menger kan een goed alternatief bieden voor stortklaar beton. Dit is een hybride benadering tussen stortklaar beton en traditionele menging op locatie. De volumetrische mobiele mixer is een vrachtwagen die beton Ingrediënt materialen en water bevat om te worden gemengd op de vrachtwagen op de bouwplaats te maken en te leveren beton volgens de hoeveelheid die nodig is. De menging in de vrachtwagen op de bouwplaats elimineert de problemen van stortklaar beton, zoals vertragingen die ervoor kunnen zorgen dat het voorgemengde beton onbruikbaar wordt.